新製品開発ストーリーStory
産学協同×固定観念の打破×AIの先駆的活用ばねのバラつき補正システム
2015年、旭精機工業では名古屋工業大学との共同研究で「ばね成形機の生産性向上システム」の実機搭載と特許取得を果たしました。熟練工の勘や経験則に頼っていた「ばねの自由長の安定化」を成形機が自律して行う同システムの開発者2人に話を聞きました。
2008年度入社
R.F
第二技術開発部主任
1991年度入社
H.S
第二技術開発部部長
熟練工の“勘頼み”ではなく機械が自律的に対応できないか
----「ばね成形機の生産性向上システム」の概要を教えてください。
H.S 押しばね(圧縮コイルばね)の量産では、ばねの自由長(荷重ゼロの時の長さ)に基づいて品質管理が行われます。自由長が同じなら“ばねの強さ”も均一だからです。しかし、ばねの形状や材質、工具が帯びる熱などで自由長にはバラつきが出やすく、これが歩留まり(良品率)を押し下げていました。
R.F そこで「成形機がつくるばねの自由長をもっと安定化したい。バラつきを抑えたい」というのが本システムの出発点となりました。
----従来のシステムではバラつきをどう抑えていましたか?
H.S 量産中のばねの自由長を1つ1つ測り、基準長さとの差をフィードバックして次の成形時に機械の動作量を補正していました。しかし、ばねは微妙で繊細なものなので、この「差」をそのまま補正値としても上手くいきません。機械の調整量はストレートに製品寸法に反映されないのです。そこで熟練工の“経験則と勘”によって一定の再計算を施し、試行錯誤を重ねて補正値を決めていました。
R.F しかし、この方法ではバラつきを十分に抑えられなかった。そこで職人の勘頼みを脱して「最適な補正値を成形機が自動算出できないか」と発想を変え、また専門的な知見を得るため名古屋工業大学と当社とで共同研究をはじめたわけですね。
名古屋工業大学と協同でバラつきの周期性を発見する
----名工大との共同研究の様子を教えてください。
H.S もともと当社では産学協同に積極的で、名工大とも関係を深めていました。そこで制御工学がご専門の水野直樹先生をご紹介いただき、当社で集めたデータの解析から「ばねのバラつきが一定の波形で繰り返されること」。つまり量産中のばねのバラつきを時系列で観察すると、そこに周期的なパターンがあることを発見したのです。
R.F いわば、従来は「点」の集合として捉えていた自由長を、連続的な「波形」として捕捉したわけですね。
H.S 先生の研究室の学生さんにも協力してもらい、私自身も何度も大学に出かけて会議に参加しました。また大学からも当社に来訪してもらい実機での作業を視察してもらいました。いわば製造現場の実情と学問性との融合の過程ですね。それで「何とかいけそうだ」となって、R.Fも含めた社内開発チームを結成したのです。
R.F チームのテーマは「バラつきの波形を正確に予測すること」。これが可能になれば、これからつくるばねのバラつきを先読みして補正できるからです。そして「予測した波形をもとに成形機をどう調整すればいいか」。これは主に制御プログラムに関する分野なのですが、私は入社5年目でソフト開発の専門家でもなく、大いに戸惑ったことを覚えています(笑)。
H.S 当社には「ジョブローテーション制度」があって、若手社員は3年ごとに別分野の仕事を経験する仕組みがありますよね。そんな社風も影響したとは思うけれど、やはりR.Fに“見どころ”があったということでしょう(笑)。実際、その後の開発作業はR.Fが中心になって進めましたよね。
補正プログラムの書き換え改善ブレイクスルーがやってきた!
----当初から順調に開発が進みましたか?
R.F いえ、まったく順調ではありませんでした(笑)。従来の制御システムをベースに「成形機が補正値を自動算出するプログラム」を組んでみました。しかし、これを実機に入れて動かすと、期待したほどバラつきが抑えられない。「理屈では正しいのになぜだろう?」と思い悩む日々が続きました。
H.S あの頃、R.Fは開発チームと製造部(組立課)を往復する毎日でしたよね。でも、われわれ“産業機械を開発する部署”にとっては、“その機械を使って製品製作のための調整をする部署”が同じ社内にあることはとても心強いですね。自分のアイデアで設計したものがすぐに実機で検証できますから。
R.F はい。製造部の皆さんには大いに感謝しています。そして名工大の皆さんとも議論を重ねるうち、ついに思い通りにいかない原因がひらめいたのです。
----ブレイクスルーのポイントは何でしたか?
R.F 当初のプログラムでは、バラつきの波形から補正値を算出し、それを成形機の動作に反映させるまでに一定の時間を要しました。補正量の算出から実際の補正までに、ばね2~3個分のタイムラグがあったのです。この2~3個分の“あやふやな部分”が全体を不安定化していたのです。
H.S それなら2~3個先ではなく“すぐ次の1個”から補正値を反映させればいい。報告を受けて「それはそうだろう」と私も同感でした。とはいえ、実際にどうやってタイムラグを解消するのか。
R.F 従来、成形機に補正をかけるには制御プログラム全体を上書きしていました。これでは時間がかかる。そこで、補正が必要な部分のみプログラムを書き換えて、それが前後のプログラムには影響しないように工夫したのです。
H.S これはコロンブスの卵のようなもので、従来の「これは全体を上書きするものだ」という固定観念を捨ててこそ達成できたものです。そして名工大をはじめ当社製造部、さらに外部のソフト開発会社など幅広い英知の結集だと思っています。
R.F 量産中に補正値を自動計算して、リアルタイムで機械に反映できる。そんな新システムの登場でバラつき補正の精度は飛躍的に向上できました。
AIやIoTの活用でアルファノマスの未来像へ!
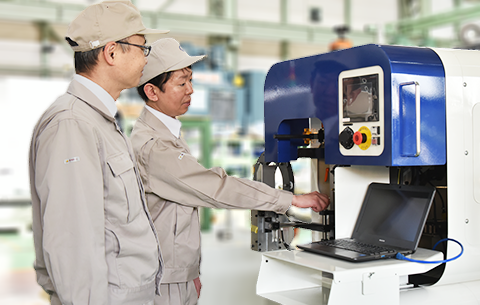
----新システムはAIとも関係すると聞きました。
H.S 「ばねのバラつきの周期性」や「機械の調整量と自由長の対応関係」の解析は、まさにAI(人工知能)の学習機能を活用したものです。本研究は「AI」という言葉がまだ一般的ではない頃にスタートしましたが、現在の視点ではAIの思考方法の根幹(ニューラルネットワーク)を活用した先駆け的な事例ともいえるでしょう。
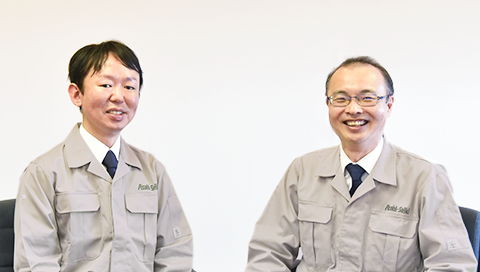
----新システムのその後と未来の方向性について教えてください。
H.S 新システムは名工大との共同出願で2015年に特許取得を果たしました。当社のばね成形機「iCFシリーズ」に搭載しての市販化も実現しています。また21年には一連の研究について計測自動制御学会中部支部から「技術賞」「産学連携賞」も受賞しました。
R.F 今後は、押しばねだけでなく、ねじりばねや引きばねなどへの展開も進めていきます。また、ばね以外の幅広い産業機械にも応用できたらいいですね。
H.S 名工大とはAIやIoT(モノのインターネット)を活用した「予知保全」の研究も進めています。これは工場内の各機械にセンサーを設置して、トラブル発生を予知して行う“転ばぬ先の杖”のメンテナンスです。
これから未来に向けて、当社では「ALPHANOMOUS(アルファノマス)」を 基本理念に掲げ、さまざまな自律機能を備えたオペレーターフリーの機械の実現をめざします。その中で、若い技術者の皆さんの活躍にも大いに期待しています。